
On the edge of the blades they welded the high-carbon steel, which was brittle but extremely hard and could therefore be made very sharp. This gave the sword an enormous toughness, almost a chewiness, meaning that the blades were unlikely to snap in combat. By separating the different types of steel, they could make sure that the low-carbon steel was used to make the center of the sword. They did this purely by how it looked, how it felt in their hands, and how it sounded when struck. The samurai innovation was to be able to distinguish high-carbon steel, which is hard but brittle, from low-carbon steel, which is tough but relatively soft. These lumps of discolored steel are very unprepossessing, but they have a whole range of carbon content, some of it very low and some of it high. At the end the tatara is broken open and the tamahagane steel is dug out of the ash and remnants of sand and charcoal.
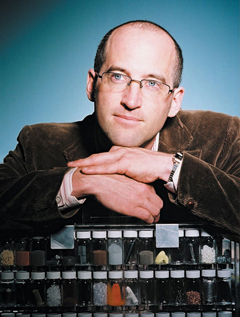
The process takes about a week and requires constant attention from a team of four or five people, who make sure that the temperature of the fire is kept high enough by pumping air into the tatara using a manual bellows. Once fired, it is packed meticulously with layers of black sand and black charcoal, which are consumed in the ceramic furnace. The vessel is “fired”-hardened from molded clay into a ceramic-by lighting a fire inside it. This steel is made in a huge clay vessel four feet tall, four feet wide, and twelve feet long called a tatara. “These samurai swords were made from a special type of steel called tamahagane, which translates as “jewel steel,” made from the volcanic black sand of the Pacific (this consists mostly of an iron ore called magnetite, the original material for the needle of compasses).
